Contents on this post
Table of contents
1. The importance of finish on guitars
Let's talk about guitar finishes. How they influence the sound of your guitar. As always, I don't pretend to be exhaustive on the subject, but I will give you some useful information if you are thinking about purchasing a new guitar. Although there are many other options for finishing musical instruments, I will only talk about the most common ones in the case of guitars: polyurethane, nitrocellulose and, finally, French polish.
The main purpose of varnish on musical instruments is to protect them. A work of fine woodwork such as a guitar —or any wooden instrument— needs to be coated with a product that preserves it from stains, scratches and knocks. The finish also seeks to prevent the wood from being exposed to other agents that may damage it, such as the player's sweat, liquids, the sun's rays, insects, etc. In the same way, in this protective facet, the varnish has the mission of dealing with humidity changes, which could cause breakage or deformation of the instrument.
But contrary to what happens in any wooden furniture, musical instruments have to vibrate (as I explain in this other post). And the varnish is a rigid product that is applied on the surface of the instrument. So if we apply a varnish on them, won't they vibrate less? The quick answer is yes: they will vibrate less. There are, in fact, examples of guitar makers who, looking for the 100% sound of the wood, left some of their guitars unvarnished, and the destructive effect of use and the passage of time on them is so evident that it seems reasonable to varnish the guitars.
So, the question about guitar finishes leads us to look for a product hard enough to protect the instrument, but at the same time flexible enough to allow the wood to vibrate freely, giving us those nuances that distinguish a low quality guitar from a high performance one.
2. Alternatives: shellac, oil, nitrocellulose, polyurethane…
In search of the ideal finish that leaves the guitar at its best, we traditionally have several alternatives: polyurethane, nitrocellulose and shellac. I will explain below what each of these options can give you. Obviously, there are more finishes available, but they are really uncommon nowadays in the classical guitar world.
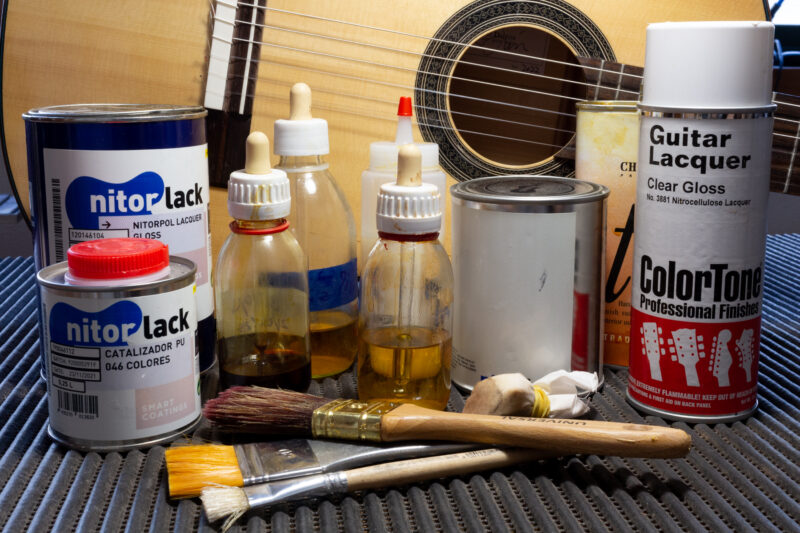
French polish, nitrocellulose and polyurethane are the main options of classical guitar finishes
2.1 Polyurethane varnish on guitars
On low-end factory guitars, polyurethane varnishes are the norm. A product that is applied with a spray gun, leaving on the wood a thick layer of a "plastic" hard enough for the guitar to withstand all kinds of inclemencies. It is relatively cheap and quick to apply, and its advantage over other varnishes is that it protects the guitar like no other, with a brightness also out of the ordinary. I would say that it is the finish that protects the instrument the most. Exaggerating a little, you can take a guitar to the Atacama Desert and half an hour later go to the wettest beach in the universe and the guitar practically doesn't even notice it.
It is the typical varnish that a guitarist who needs to tour the world with his guitar would ask for. In fact, it is not uncommon to see this type of varnish on the big stages of mainstream bands. It makes sense. Touring is such a crazy time of environmental changes, travel, dangers of bumps on stage setups and teardowns, and so on, that it's a good idea to bring an all-terrain instrument with you.
The disadvantages, on the other hand, are not small at all. It is risky to expect an instrument that has a thick layer of fairly hard plastic applied on top of it to vibrate freely. In my opinion, if we want to get a good sound —a sound with nuances— this varnish should be directly discarded. Of course this depends on your preferences and what you want to use your guitar for.
Another disadvantage that for me is important is that repairs are not easy on this type of guitars, precisely because of the varnish. Although there are tricks to avoid this, any repair, no matter how simple, will most likely be noticed. Even if it is just gluing a small crack or blow on the top, or a profile that has peeled off. The repair can be done, yes: but there will be a "scar", either because of differences in color, or because the repaired part shines less brightly. I spend a good part of my workshop hours repairing guitars with this finish and I always have to warn the customer about this.
The point is that to properly repair a finish of these characteristics and that it is not noticeable, what would have to be done is to remove all the varnish from the part to be repaired, make the repair and replace all the varnish again. Something that requires a properly conditioned workshop, some specific machinery and above all protection for the luthier, because when applying the polyurethane a series of vapors are released that are extremely toxic. For a small workshop like mine, this is practically impossible.
2.2. Nitrocellulose varnished guitars
The second classic option are nitrocellulose finishes. This is also a synthetic product, also applied with a spray gun. The level of protection is quite high and a good finish can be obtained with a fairly small layer of varnish, which gives it advantages over polyurethane in terms of sound. Here the wood can already vibrate with a certain freedom. It is the varnish typical of some high-end guitars, very present in steel string acoustic guitars.
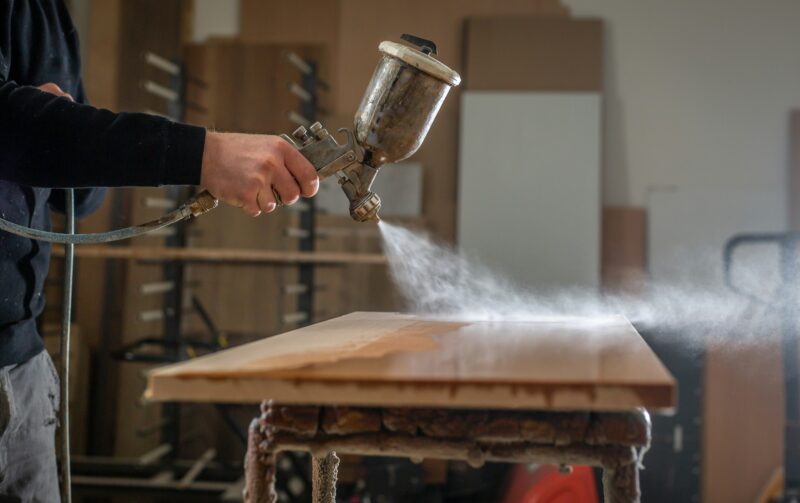
Both nitrocellulose and polyurethane must be applied using a spray gun, and that requires having an appropriate spray booth to avoid toxic vapors generated when varnishing
It is, however, a finish that is laborious to obtain, as it consists of applying tiny layers of lacquer one on top of the other, with notably long drying times. In terms of repairs, we have a situation that allows repairs to be made with minimal impact on the final appearance of the instrument. However, obtaining this level of perfection by matching the old varnish with the new one requires great expertise and a lot of experience, and it is also advisable to apply it over the whole guitar.
Many high-end factory guitars are varnished with this type of finish. It is not a bad option, as long as the manufacturer has taken care to apply as little varnish as possible. It is, at the same time, a varnish that deteriorates with the passage of time, being frequent that it gets corrupted and "cracked", appearing the so-called crackle effect, which lately is very fashionable in the so-called "relic" electric guitars, in which the aim is to obtain the effect of old varnish on new guitars. Something similar to what happens with the jeans that you buy already worn out…
2.3 French polished guitars
Shellac varnish is also called French polish. This type of finish is the one I personally apply to my guitars. Contrary to the varnishes I explained above, shellac is a natural product. It is obtained from a resin that generates the so-called shellac cochineal (here is a link to the Wikipedia entry). After further processing, flakes are obtained which, mixed with alcohol, are the most common finish of high-end classical guitars. And I'll explain why.
First of all, it is the one that best enhances the sound. It is a layer of varnish so small, so small, so small, that with a fingernail and without much force you can take it away. The wood vibrates freely here, as it is an organic product with a considerably lower hardness than polyurethane or nitrocellulose. Something that you could only get with some oil-based varnishes, which I will not talk about for not making this post too long, although its advantages are very comparable to shellac. But the fact is that with a guitar finished in shellac you will have all the nuances present in the work done by the luthier, without exposing yourself to the risk that the varnish is "covering" them.
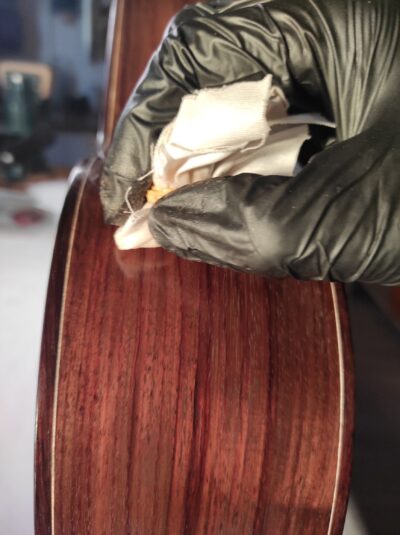
French polish is applied rubbing a "muñeca" damped on shellac and alcohol on the guitar.
Secondly, it is a hand-applied varnish, minimally toxic and relatively easy to apply, although obtaining a good level of gloss is by no means an easy task. The process of French polishing is a long one. During weeks, coats and coats of varnish are applied (dozens of micro-coats), with quite long drying times. To give you an idea, it takes me about a month to varnish a guitar with this technique. A pain, yes, but I insist: in my opinion French polish will be the varnish that best enhances the sound of your guitar.
The third advantage is that repairs to the instrument are quite simple. If done properly, it is enough to apply a little shellac on the repaired area, so that the new varnish blends with the old one, being perfectly invisible in the final appearance of the instrument. On the other hand, it is a finish that requires periodic maintenance. That is to say, it will wear out with use and time, and from time to time the guitar will have to go to the luthier to apply new coats of varnish.
It is true that shellac is delicate, but its advantages are so remarkable in terms of sound that it is rare to find high-end guitars varnished with another product. The instrument lacquer industry has been trying things out for years, and I personally have yet to try one that matches shellac in its ability to preserve the nuances in the sound.
2.4 Shellac and nitrocellulose varnished guitars
There are guitar makers who choose to do a mix of varnishes on their guitars, applying shellac on the top and varnishing the rest of the guitar with polyurethane or nitrocellulose. It is not a bad option, if we consider that the top is the most acoustically important part for the sound of the instrument. Personally I do not apply it because of the need to have machinery and a room adapted to apply synthetic varnishes. Besides, the advantages that shellac has when repairing guitars seem to me so remarkable that I don't find much profit in mixing finishing techniques.
3. Conclusion
Maybe this post has been too long, but I hope it has helped you to differentiate the most basic varnishes that we find in the guitar world. Understanding what each one gives you I think it can help you to make the decision of what guitar you need. As my preference is for shellac, here is another post in which I explain some specific care that shellac needs.
David: Thank you for this. I have been using French-polished shellac for nearly twenty years. It never fails, although sometimes it is stubborn! I would love to read your information about oil varnish: making, pre-made, application, results, etc. Thank you.
Hi Scott, thanks for your comment. Well, I’m not really specialized in oil varnish, although some colleagues using oil varnish as a guitar finish say that it has some of the advantages of French polish in terms of sound and maintenance, but not the same mirror-shiny looking.